[LEGACY] Multiaxial Control with Constant Strain Rate
This example (tutorials/triaxSLR
) covers the biaxial deformation of an HCP polycrystal at a constant strain rate. Loads are applied normal to the surface, maintaining proportional macroscopic load ratios of \(-1\):\(0\):\(1\) for the \(x\):\(y\):\(z\) directions, respectively. Load tolerance options are prescribed and latent hardening is enabled, as well as saturation strength evolution. The primary loading direction is set to be in the \(x\) direction, and the strain rate is doubled on the second step. Elemental values for the equivalent plastic strain and plastic work are output, along with the nodal coordinates and surface-integrated forces. Material parameters are those for the \(\alpha\) phase of Ti-6Al-4V and are provided in the below tables. The latent parameters are input values to the hardening interaction matrix [CARSON17]. Illustrations of the results are provided in the below figures.
Phase |
Type |
\(C_{11}\) [MPa] |
\(C_{12}\) [MPa] |
\(C_{13}\) [MPa] |
\(C_{44}\) [MPa] |
---|---|---|---|---|---|
\(\alpha\) |
HCP |
\(169.66 \times 10^3\) |
\(88.66 \times 10^3\) |
\(61.66 \times 10^3\) |
\(42.50 \times 10^3\) |
Phase |
\(m\) [-] |
\(\dot{\gamma_{0}}\) [1/s] |
\(h_{0}\) [MPa] |
\(g_{s0}\) [MPa] |
\(m^\prime\) [-] |
\(\dot{\gamma_{s}}\) [1/s] |
\(n\) [-] |
\(c/a\) [-] |
---|---|---|---|---|---|---|---|---|
\(\alpha\) |
0.01 |
1.0 |
190.0 |
530.0 |
1.1 |
1.0 |
1.0 |
1.587 |
Phase |
\(g_0\) (basal) [MPa] |
\(g_0\) (prismatic) [MPa] |
\(g_0\) (pyramidal) [MPa] |
\(h_{diag}\) [-] |
\(h_{1}-h_{7}\) [-] |
---|---|---|---|---|---|
\(\alpha\) |
390.0 |
468.0 |
663.0 |
1.0 |
1.4 |
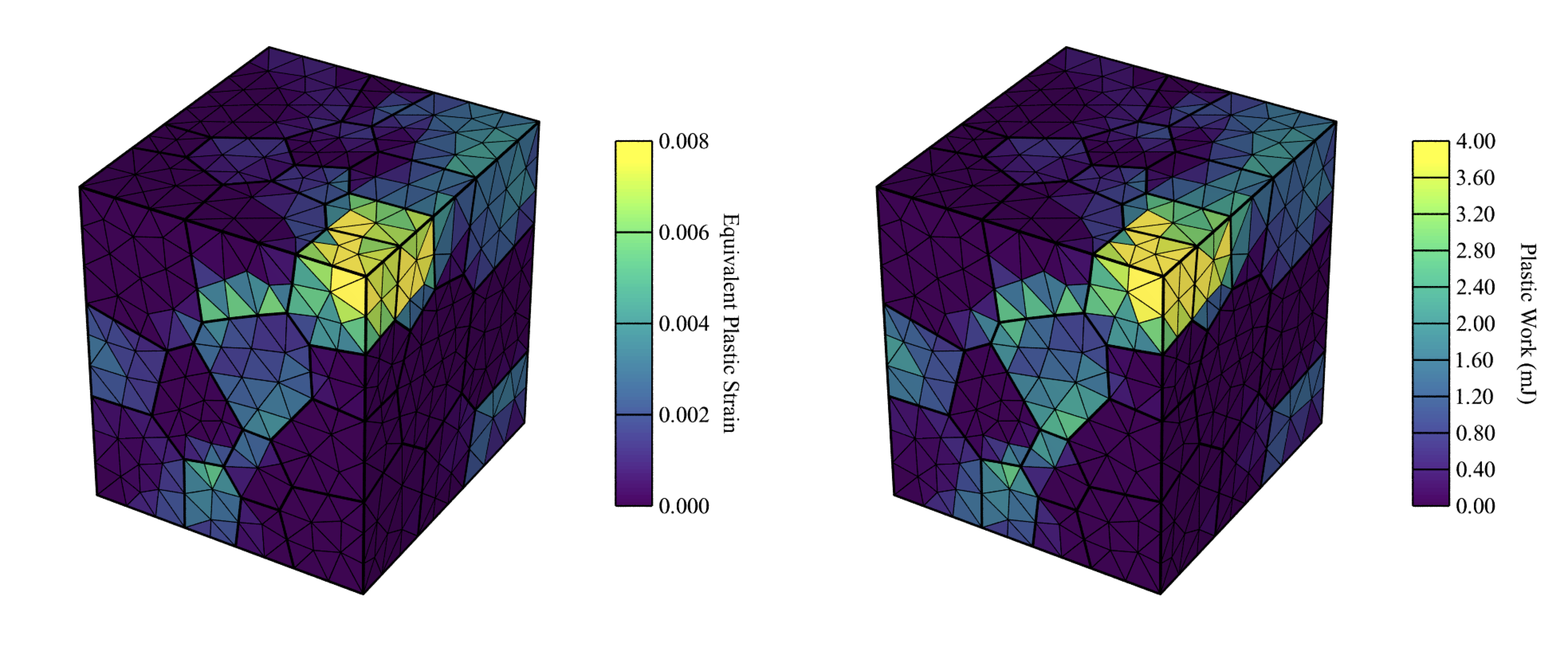
Deformed sample at the end of the second load step (deformation field is exaggerated 10x for illustrative purposes), colored by (left) plastic work (\(W^{p}\)) and (right) equivalent plastic strain (\(\bar\epsilon^{P}\)). Note that, unlike the deformed sample in uniaxial_ex, a multiaxial simulation will maintain the orthogonal, planar surfaces throughout the simulation.
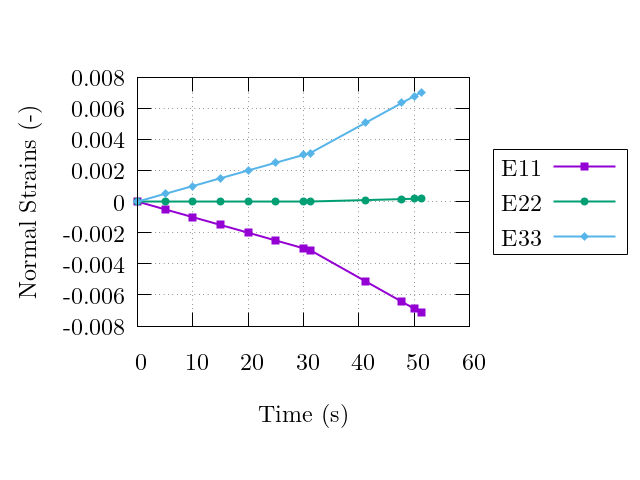
Evolution of the macroscopic normal strains. Note the strain rate increase corresponding to the strain-rate jump defined for step 2.